E-Coat Process
Enviro-Strip GB Ltd.’s auto restoration customers now have the added option of adding a long term rust protection coating to their body-shells electrophoretic or ‘e-coating’ as it’s more commonly known.
E-coating is applied to the vast majority of the new cars produced today throughout the world and is specifically designed to provide protection against mild steel corrosion. E-coating, involves fully immersing the body-shell in a range of cleaning and phosphating solutions before passing into an electrically charged tank, once submerged a current of around 400 Volts is passed through the tank causing the paint to uniformly bond to all areas of the shell.
The process is best carried out once all welding / repair work has been completed on the body-shell & will help in give classic car owners many more years to enjoying their pride & joy.
Pre treatment & E coat process
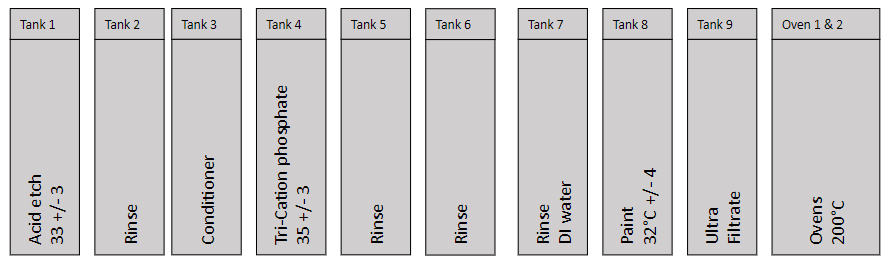
Working Envelope: 7.6m(l) x 1.8m(w) x 2.7m(d) at 2 tonnes
Stage Description
Stage 1: R-Clean 705
R-Etch 601 is a Acid etch submersion bath designed to clean any light oils and grease of the
work piece and chemically remove surface rust and laser oxide.
Stage 2: Towns Water Rinse
Stage 2 is a submersion tank to remove any chemical that may have been retained on the
surface of the work piece.
Stage 2A: Towns Water Halo Spray
Stage 2A is a spray stage to ensure that the carry over of any chemical is kept to a minimum.
Stage 3: Activator CT
Activator CT is a conditioning bath to chemically prepare the surface of the work piece for
the Tri-Cation Phosphate bath.
Stage 4: R-Phos 401
R-Phos 401 is a Tri-Cation (Tri-Cat) phosphate which applies a corrosion protective coating to
the work piece that restricts any corrosion from spreading or creeping under the paint.
Stage 5 and 6: Towns Water Rinse
Stage 5 and 6 are submersion baths to remove any chemical that may have been retained
on the surface of the work piece.
Stage 7: De-Ionised Rinse
Stage 7 is a De-Ionised water submersion tank that remove any heavy metals that may be present on the work piece from the towns water. Stage 7 is also fitted with a halo spray to help with the removal of the heavy metals prior to the painting stage.
Stage 8: Aqua EC3000
Aqua EC3000 is a cathodic electrophoretic paint (E-Coat) from Axalta the work piece is submersed in the bath and connected to the negative side of a electric circuit the paint particles are slowly positively charged using a rectifier. The positive charged paint particles build up on the negative work peace till it reaches a thickness that it becomes nonconductive to the pre set volts. This ensures an even film build thickness over the whole surface of the work piece that is controllable by the amount of volts put in to the paint partials.
Stage 9: Ultra Filtrate (UF) Rinse
Stage 9 is a submersion bath, Ultra Filtrate is filtered from the E-Coat bath and pumped to
the UF bath which overflows back to the E-Coat bath. The continuous overflow of the UF
bath means that any unbounded E-Coat that was carried over is return to the E-Coat bath.
Stage 9A: De-Ionised Water Halo
Stage 9A is a halo spray ring above the UF bath it operates when work is going in and out of
the bath and is used to ensure all unbounded E-Coat is washed of the work piece.
Stage 10: Gas Fired Cure Oven
Stage 10 is a well oven design and cures the work piece for 40 minutes with a air
temperature of 200 degrees. The cure interlocks the paint particles and hardens the
Coating a process known as Cross linking.